What Is the Inverter and How It Works
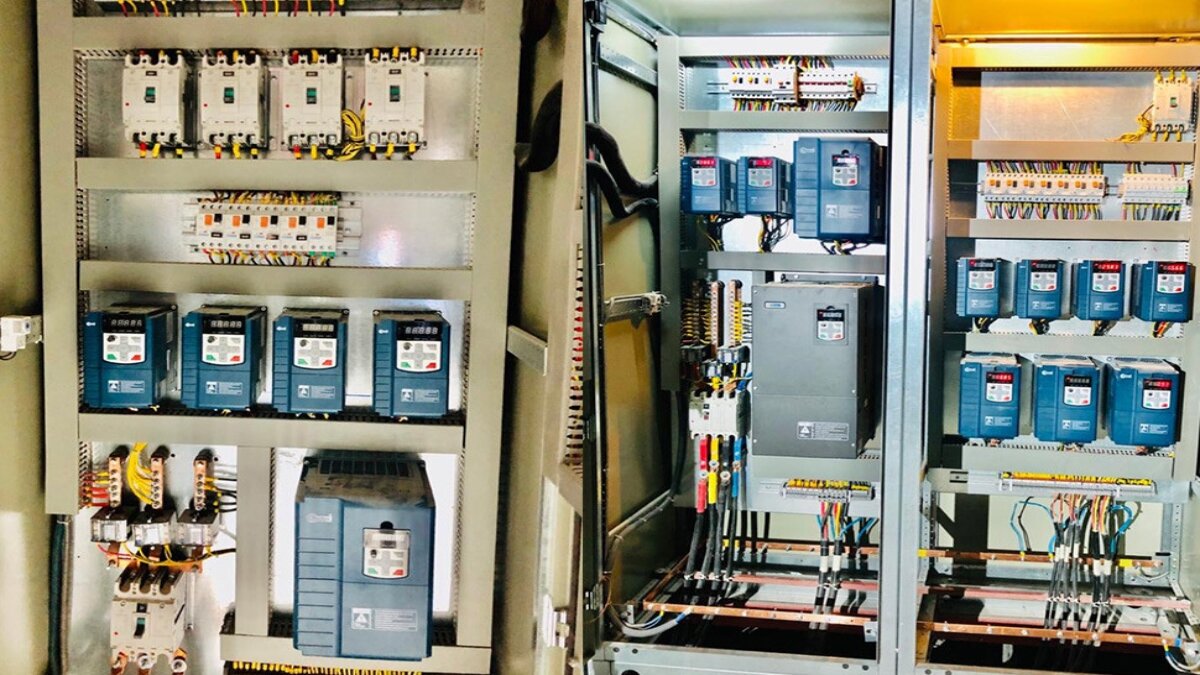
The significance of an inverter or converter cannot be overstated in various industries, as it serves as a crucial electrical apparatus that transforms power to a higher voltage level. But the questions are how the inverter works and what is the application of inverter in the industry. In this article, we'll deeply delve into the details of this electronic device to find answers to these questions.
What Is the Inverter?
An inverter is a smart electronic gadget that transforms the steady flow of direct current (DC) power into the alternating current (AC) power we commonly use. It ingeniously takes the input from a DC source, like a battery or a solar panel, and skillfully converts it into AC power, which is indispensable for operating a vast array of devices and appliances.
Converters are available in various sizes and capabilities, tailored to suit specific purposes. They can be compact and easily transportable, catering to personal electronic devices or appliances. On the other hand, they can also be more substantial, and seamlessly integrated into power systems for residential, commercial, and industrial environments. The effectiveness and excellence of the alternating current (AC) power produced by converters may differ based on their type and design.
In essence, inverters play a pivotal role in facilitating the utilization of direct current (DC) power sources, ensuring compatibility with the AC devices we rely on in our everyday routines.
Types of Inverters
There are various types of inverters available, each specifically designed for different applications and power requirements. Some of the most commonly used types are as follows:
String Inverters
These converters are primarily utilized in grid-tied solar power systems. Their main function is to convert the direct current (DC) generated by solar panels into alternating current (AC) that can be used in homes or businesses.
Microinverters
In contrast to string inverters, microinverters are installed on each individual solar panel rather than being connected to multiple panels in a string. This allows for more effective monitoring of performance and optimization of each panel's output.
Central Inverters
These large-scale converters are predominantly employed in utility-scale solar power plants. They are responsible for converting DC power from multiple solar arrays into AC power, which is then distributed to the electrical grid. Various companies produce this type of converter, and Siemens inverter is considered one of the best of them.
Battery-based Converters
These are also known as inverter-chargers and are intended for use in off-grid or hybrid solar power systems. In addition to the common purpose, which is converting power, these inverters have the capability to charge the batteries by utilizing AC power from an external source.
Grid-tie Converters
These converters are specifically designed to synchronize the AC power they generate with the electrical grid. They are commonly employed in residential or commercial solar power systems to offset the consumption of electricity from the grid.
Stand-alone Inverters
Stand-alone converters are utilized in off-grid solar power systems where access to the electrical grid is unavailable. Their function is to convert the DC power generated by solar panels or stored in batteries into AC power, which can be utilized in standalone applications such as remote homes, cabins, or RVs.
Modified Sine Wave Converters
Inverters that produce a modified sine wave create a simplified version of AC power known as a sine wave. Although they are usually cheaper, they may cause harmonic distortion and may not work well with certain sensitive electronic devices.
Pure Sine Wave Inverters
Pure sine wave converters, on the other hand, generate a clean and unadulterated AC output that closely resembles the power provided by the utility grid. These converters are perfect for operating delicate electronics and equipment without any potential for harm or malfunction.
How Does an Inverter Work?
The fundamental operational principle of an inverter involves several stages:
1. Rectification
Initially, the incoming AC power is converted into DC power by means of a rectifier. This conversion process is typically achieved using diodes, which permit the flow of current in a single direction.
2. Filtering
The rectified DC power often contains undesirable elements, such as voltage fluctuations or ripples. To smooth out the output, a filter is employed to reduce these fluctuations and provide a more stable DC voltage.
3. Conversion
The filtered DC power is then directed into an electronic component known as an inverter circuit. This circuit comprises power switches (typically transistors or insulated gate bipolar transistors - IGBTs) that regulate the flow of current.
4. Pulse Width Modulation (PWM)
The converter employs a clever technique known as Pulse Width Modulation to convert the direct current (DC) power into a high-frequency alternating current (AC) signal. By adjusting the width or duration of the pulses, PWM effectively regulates the output frequency and controls the amount of power that is delivered.
5. Output AC Signal
Subsequently, the inverter circuit transmits the high-frequency AC signal through an output transformer, which either steps up or steps down the voltage levels depending on the specific application. This process ensures that the resulting AC voltage and frequency are tailored to suit the requirements of the device or system being powered.
6. Output Filtering
Similar to the filtering stage during rectification, the output AC signal typically undergoes filtration to eliminate any remaining harmonics or unwanted noise before it is supplied to the load. This ensures that the delivered power is clean and free from any undesirable distortions.
Applications of Inverters in Industries
Inverters are vastly used for controlling electromotors in different machinery varying from pumps, conveyors, compressors, mixers, and fans. They adjust the motor speed and voltage to suit specific operational requirements. Some of other applications of converters are as follows:
- Achieving variable speed control
- Increasing engine speed control or RPM control
- Enabling soft start and stop
- Offering direction control
- Promoting energy efficiency
- Ensuring precision control
- Integration of renewable energy
- Variable Frequency Drive (VFD)
- Electric vehicle charging
- Power conditioning
- Rail traction systems
Leave a Comment