Siemens says to focus on infrastructure projects in Iran
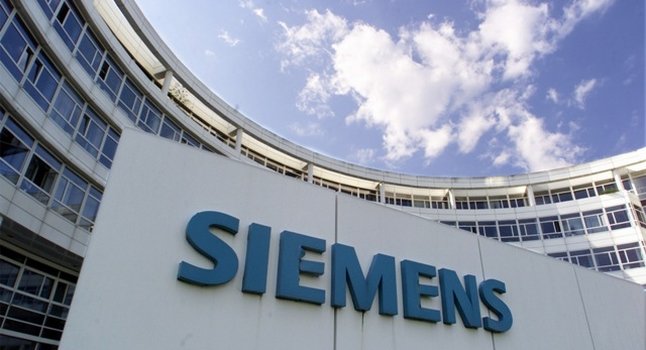
I had a chance as the first Iranian journalist to visit the new headquarters of Siemens in Munich.
There, I met Mr. Yashar Azad, Group Spokesperson at Siemens AG, interviewing him about history of activity of Siemens in Iran and its outlook for the future.
Below is the full text of the interview with Mr. Azad.
I would like to start asking you about Siemens and Iran. Do you think we will see a new era of relationship between Siemens and Iran in post-sanctions era?
Siemens started its activities in Iran in 1868, so we have a history of almost 150 years in the country. Our operations began with the telegraph line from London to Calcutta via Tehran. So we have a good and long-term partnership with Iran. We always had 100 people here and continued the execution of projects in the frame of international rules and regulations.
We maintained our office and infrastructure in the country as well as the relationship with our customers. After the easing of sanctions, new doors have opened for Siemens, and we know that the country needs new equipment, has to invest in new projects, and has requirements for new technologies.
Our main focus areas after the easing of sanctions are the infrastructure projects, the supply of equipment and technology, and know-how transfer. Our strategy is to be a sustainable partner for the country and support the development of infrastructure and industry.
Would you tell us the vision of senior managers of Siemens about transferring technology to Iranian engineers and share experiences in the field of oil, gas and energy?
As you know, Siemens has signed a far-reaching agreement with Mapna in the gas turbine sector. The long-term technology license agreement between Siemens and Mapna is for the local manufacturing of Siemens F class gas turbines by Mapna in Iran.
Under the terms of this agreement Mapna will work with Siemens to deliver F-class gas turbines and associated generators into the Iranian market and defined neighboring countries. The first six gas turbines will be completely manufactured by Siemens and then we will gradually shift the value add to Mapna.
We have shipped the first F-class gas turbine for the project Bandar Abbas to Iran on Sep. 20. 2016. This is the first stage of the bilateral contract covering the transfer of know-how for F-class gas turbine technology between Siemens and Mapna.
Would you tell us if Siemens will develop wind power technology in Iran?
We now have a local wind power team in Iran and we are very optimistic that this will mark the starting point of a successful development of our wind business in Iran. Iran has very good wind conditions and the government has set ambitious targets with 5 GW of installed wind power capacity by 2023 supported by a clear incentive system.
Siemens has already been selected as preferred supplier for a 62 MW project in Iran which will contribute towards diversifying the energy mix in the country. We are proud to support these ambitions with innovative and reliable technologies.
Why Siemens switches from b2c to b2b model.
Pioneering technologies and the business models that build on them are the foundation of our success. Our core business was always more on electrification and automation.
We have only stayed profitable because we have reinvented ourselves several times. Leading positions in technology provide a decisive competitive edge. That is why we are continually striving to achieve leadership roles in the areas of electrification, automation and digitalization.
Would you tell us about Siemens’ plan to move toward the Internet of Things?
Siemens foresees great opportunities from the Internet of Things. The value of the IoT lies in connecting the real world with the virtual world of data.
Digitalization technologies offer new business models here. For example: we have a division called digital factory, where we merge the real world, which is hardware, with the virtual world, which is simulation software. We have all the elements of manufacturing automation in that division. We have hardware such as control systems and CPUs. Then, around that hardware, we have so-called PLM (product life-cycle management) software, which allows us to simulate production and robotics flows ahead of time. So today, we build manufacturing automation lines and design processes before a manufacturing plant has been built.
Merging the real world with the virtual world allows us to create what we call a digital twin. We copy a real-time manufacturing process into the virtual world to optimize engineering, processing quality, uptime, and load time — and then we copy it back into the real world of manufacturing.